Capture Fumes and Dust to Maintain a Safe Workplace
Plasma cutting is a volatile and dangerous process. Operating a plasma cutting machine safely requires training and skill, but it also requires a properly maintained work environment.
The process of plasma cutting creates fumes, smoke, dust, and sparks that must be collected and controlled in order to keep workers safe and to maintain optimal indoor air quality.
Because all facilities present their own unique characteristics, installing an ideal extraction system is not a one-size-fits-all process.
Variables in plant infrastructure make proper planning a crucial part of the installation process. All plasma cutting hazards need to be addressed – for your employees and to preserve your investment in a plasma cutting machine.
Summit understands the hazards and has the engineering expertise to design the perfect system for your facility’s health and safety needs.
Water Tables vs. Dry Collection. Plasma Cutting’s Unique Faceoff
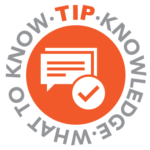
Whether using hand-held plasma guns or robotic plasma cutting machines, plasma cutting is always a job that requires dust collection and fume extraction. Harmful smoke and small particulates – which are especially small and hazardous due to the high temperature of the plasma cutting machine process – are potential health and safety impairments that must be handled with dust collectors and ventilation systems.
Selecting the right system is a particular challenge because of the sparks created by the high pressure and high temperatures of the process.
A water table may not be the answer
Sparks and large amounts of smoke are reasons that many companies with plasma cutting machines choose to utilize water tables underneath their workspaces. Water tables extinguish sparks and bits of molten metal, preventing them from causing damage and creating more hazardous smoke.
The effect of water is a strong positive, but there are consequences. Potential downsides include:
- Steam and moisture can clog your plasma cutting machine’s torch head and lead to overheating
- Water can create ripples (or striation) which affect the quality of cut edges
- Water grounds the plasma arc, which can make for less accurate cuts
- Aluminum and water can react to produce hydrogen gas pockets underneath a plate being cut, which can lead to an explosion
- The equipment’s mild steel elements are all more subject to rust and degradation
- Leakage and spillage from a water tank can cause slip and fall hazards in your plant
- Chemical stabilizers, rust inhibitors, and maintenance time will all be necessary to keep the water clean
Dry systems avoid the pitfalls of a water table
While you can install ventilation systems that will work around your existing water table, the water does limit your flexibility when installing the ducting and dust collector you will need to properly collect fumes and particles.
Summit can actually install a dry system where spark traps are built into the ducting. It will satisfy your need for dust collection and ventilation, and eliminate concerns about sparks.
Ultimately, a dry ventilation system can save you money and avoids the potential downsides of a water table.
Did you know metal dust particles left uncollected easily find their way into exposed eyes?
It’s a common cause of injury in factories. Source capture can help.
Factors to Consider When Designing a Plasma Cutting Ventilation System
A ventilation system can only be as effective as the planning behind it. When it comes to compliance and safety, you must ask all of the pertinent questions and consider all of the little factors that make your facility unique.
- How tight is the floor space around your plasma cutting machine or machines?
- Does your facility employ robotic plasma cutting machines or manned plasma guns?
- What type of metals will you be cutting, and is the dust from these metals combustible?
- Will you use water tables going forward?
- Which option is the most energy efficient and cost effective?
These questions are for starters. The process of designing the correct ventilation system for your facility is complex. Never entrust your indoor air quality to anyone but leading industry experts.